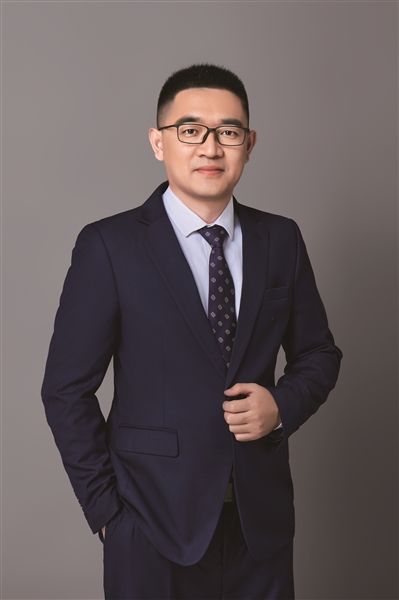
杭州博岳生物技术有限公司创始人 李因来 新质生产力在生物医药产业中的应用和发展,不仅推动了技术创新和产业升级,也为其可持续发展提供了强大的动力。我认为,新质生产力的核心就是以技术创新实现对行业的再升级,博岳生物的技术创新就体现在生物医药上游核心材料的开发、应用及产业化中,我们力求瞄准生物医药上游“卡脖子”和高壁垒等赛道,为国内生物医药产业升级研发出有价值的产品。
编者按:即日起,本报联合杭州市科技局共同推出《“新”青年·这YOUNG说》栏目,讲述青年科技人才如何以独特的视角和创新能力,引领新质生产力的变革,推动科技与产业的深度融合。
商报记者 黄诗睿
无论是职业经历,还是生物研发经历,李因来都算得上资深。早年读研,毕业后进入生物医药知名企业工作,在研发技术、市场营销等一线岗位深耕近十年,中途还经历了两次连续创业,都聚焦于IVD(体外诊断)领域并取得了不错的成绩。
2018年,李因来成立杭州博岳生物技术有限公司(简称“博岳生物”),聚焦于IVD试剂原料的研发和生产,并将制约我国工业发展的35项“卡脖子”技术之一的微球制备技术作为重点研发技术,推出自主研发的免疫磁珠产品,成功实现国产替代。
“免疫磁珠有着优异的磁响应性、生物相容性及化学稳定性,一直被广泛应用于疾病的检测,在IVD领域,其主要运用在化学发光、分子诊断和细胞分选等方面。”李因来介绍道,彼时,国内生产的免疫磁珠存在批间差异大、应用上灵敏度低、单批次产量低等痛点,几乎都要依靠进口,然而国外的免疫磁珠1g价格在12000元以上,成本高、用量大,进行自主研发刻不容缓。
据李因来介绍,免疫磁珠的研发瓶颈主要在于精准制备与包覆技术,他们用近两年的时间研发了一款核心技术,较好地解决了国内免疫磁珠存在的大部分问题。2020年8月,博岳生物自主研发的化学发光免疫磁珠正式面世。“我们找国内化学发光试剂公司评估,他们第一反应都是‘国产免疫磁珠性能差,没有测试的必要’,测试使用后他们感叹道,‘你们的免疫磁珠在稳定性、信号值、灵敏度等核心指标上已经达到与进口产品品质相当的水准。’”
在企业中,李因来既是领导企业不断向前的领头羊,更是产品定位与研发的主心骨。早在企业成立之初,他就综合考虑了产品差异化、研发效率等问题,事实证明他的选择是正确的。目前,企业的免疫磁珠产品已经更新至第五代,单批次产量5kg,年产量100kg,市场占有率在国产品牌中处于领先,更是拥有不少战略级别合作的大客户,在测试精密性等指标方面甚至更胜进口产品一筹。
如今,博岳生物在IVD领域是全球为数不多的实现免疫磁珠工业化的品牌之一,而通过对单克隆抗体、多克隆抗体和基因工程抗体等生物活性原料的布局,其也成为了国内极少数拥有纳米材料与生物活性原料双自主产业化平台的生物医药上游企业。李因来坦言,这是企业实践多学科深度交叉融合的结果。
2018年成立至今,企业以生物化学、分子生物学、高分子与材料学、细胞工程学、免疫学和生物信息学为基础,已形成覆盖生物医药全场景的六大技术综合平台。“我们的平台指的是包括原料开发、原料规模化生产、原料迭代升级在内的全链路平台。”李因来解释道,“目前,我们的产品和服务线以IVD核心原料、生物医药纯化填料和IVD整体解决方案为主,优势在于已经实现了95%的自研生物原材料使用率,涵盖抗体、抗原、生物酶和纳米微球。”